In fenestration, you can often hear statements like ‘dead air is the best insulator’. That’s pretty close to the truth, and the reason most windows are made hollow.
However, air is not 'dead' but a fluid. Unlike direct heat transfer in solids, it is convection that accounts for most energy transfers in fluids. The water vapor contained in air is an aggravating factor. The transition of water between states — freeze-thaw, condensation-evaporation — is so energy-intensive that it's responsible for at least 40% in the total heat exchange happening in the atmosphere. And that's with a tropospheric water content of less than 1%! Making air truly 'dead' for insulation purposes means eliminating convection and water vapor altogether.
To reduce heat loss by convection, manufacturers add more chambers to hollow windows. It splits the frame into several consecutive interior chambers, limiting convection locally. The more chambers, the better. Our microcellular PVC windows DO have chambers inside, and not just a handful: there are BILLIONS per window, but only about 50 micrometers in size. It makes for better insulation – no convection, no condensation. That’s the reason why nobody leaves their walls hollow anymore, with closed-cell insulation outperforming all other types

Painted, foam-filled PVC window. Injected foams help reduce heat loss through convection. However, they cost more and need more quality control. Chemical foams have adverse effects on health and the environment. Paint contaminates the PVC, reducing its reuse value. Injected foams don’t allow for a mechanical separation of materials so these windows aren’t recyclable, ending up in landfills.
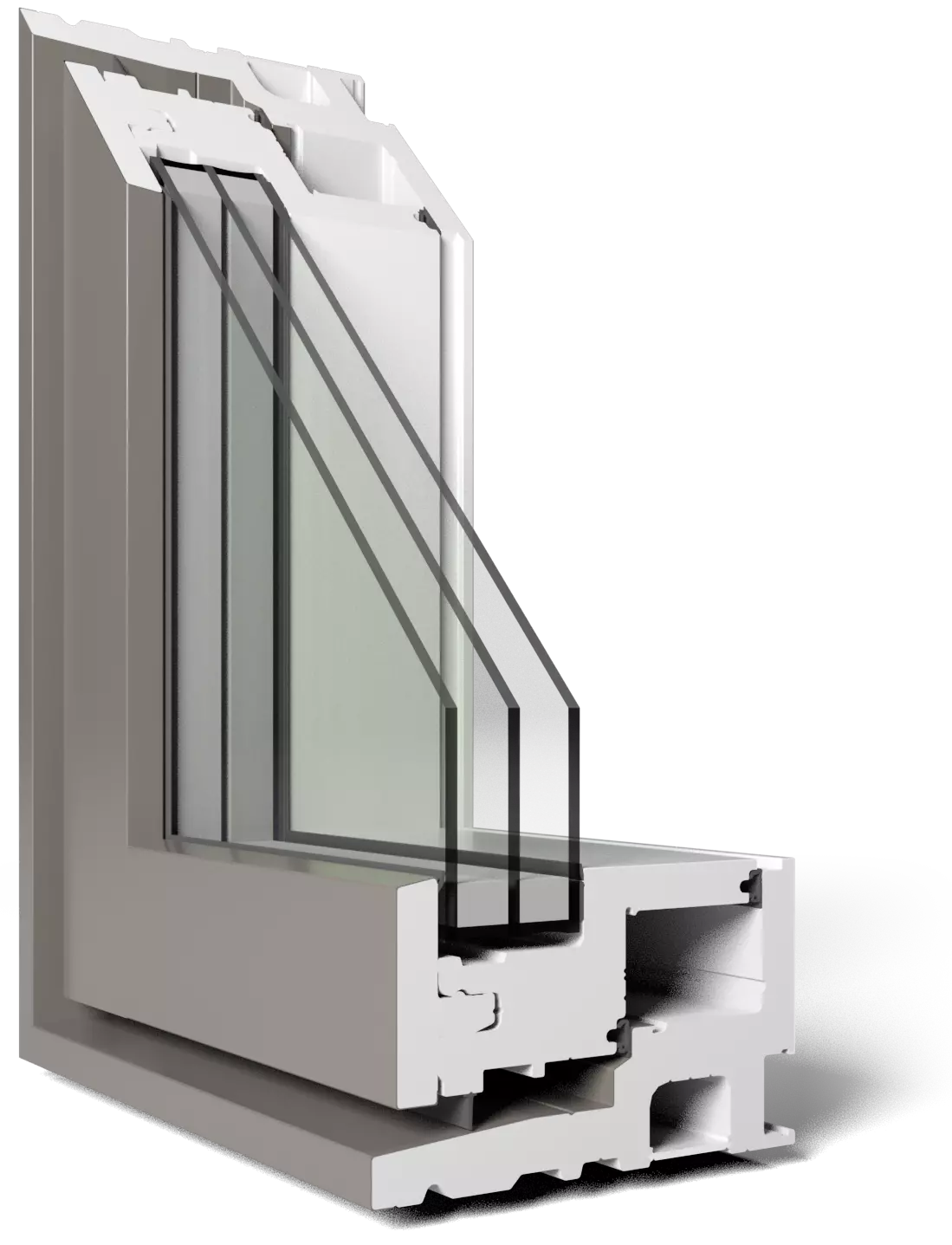
Cap-stocked microcellular PVC window. Microcellular PVC is a built-in insulation without convection or condensation issues. The solid construction is more durable, as well as more airtight from stronger corner welds. Since the structural member, capping, and insulation is one material, it can be mechanically separated for recycling and reuse without degradation of properties.
Most PVC window manufacturers today stick to bulky hollow extrusions, but fill them with insulating foams. This workaround comes with drawbacks. The steps added to the manufacturing process mean higher prices. Injecting liquid foams after the window is assembled doesn't allow for adequate quality control: smaller cavities are left unfilled, the foam does not fill uniformly, and it can deform the thin-wall construction of the frame. Pre-filling PVC extrusions with foam before the window is assembled makes for a weaker - and messier - fusion weld at the corners. Another approach is inserting solid foam blocks into frames, but these don’t fill the entire cavity, so convection and water vapor aren't fully eliminated. There are also environmental and health concerns with many foams' chemical formulations: chlorofluorocarbons (CFCs), hydrochlorofluorocarbons (HCFCs) and halons destroy the earth's protective ozone layer, while volatile organic compounds (VOCs) have short- and long-term adverse health effects.
We invested years into developing our RevoCell windows. We wanted to make them more energy-efficient and stronger, while keeping them affordable. We ended using the same tried and tested PVC formulation any decent window manufacturer would — pure unplasticized PVC. What we did differently was turning it into a microcellular structure. Think polystyrene foam (Styrofoam), but hard as bone, and with smaller cells. The gas trapped inside is ubiquitous non-toxic carbon dioxide, with zero water vapor. CO₂'s molar mass is higher than that of the air mix, meaning reduced convection; its large molecular size prevents escape from the polymer. It insulates so well that a microcellular PVC window can exceed the ENERGY STAR Most Efficient designation - the highest official rating in Canada - even with dual-pane glass.
Microcellular PVC is not only an excellent thermal break, it also allows for solid structural members. Its screw holding power is better than most woods, preventing failure due to wear at the interface with metal hardware. The cellular structure absorbs shocks and distributes loads better, not just along the extrusion as in hollow windows, but also across - where the largest forces are actually applied. As a result, our RevoCell casement windows have a NAFS Performance Grade of 85 - levels above the best competitors. They also have a forced entry resistance rating of F40 - North America's highest.
Are RevoCell windows a more sustainable alternative to hollow foam-filled windows? We’ll let you judge. Their construction is done in one material – inside and out. The interior is microcellular PVC. The exterior surfaces are capped with the same unplasticized PVC as the interior but solid, tinted to provide a permanent finish that won't wash off, flake, or fade under UV exposure. No paints, no pollutants. Since the capping is engineered in one piece with the structural and insulating member, it is made of the same material, and is recyclable several times over without degradation of properties – with adequate mechanical separation of course. Without injected foams, microcellular PVC is also free from CFC's or VOC's which are harmful to health and the atmosphere.
We’ll be honest: microcellular PVC windows aren’t the apex of evolution. Man has perfected the use of solids for large load-bearing structures - concrete, steel, glass - for centuries. Nature, on the other hand, has used cellular structures in living beings for much longer – take wood, coral, or bone for example. Turns out, there are good reasons for it, as we tap into the potential of microcellular materials. A return to the natural course of evolution, that's a revolution. It's what RevoCell stands for: it's revolutionary, and it's cellular. And we're always improving it.